|
|
PRODUCTS |
Built in brushless DC planetary gear reduction motor drive |
Tubing rotator |
|
|
|
|
The problem of oil pipe partial wear, especially the oil pipe wall of inclined Wells, is a practical problem that troubles each oil field in the process of oil production. However, this problem has been overcome by R & M Energy since 1941, and has been widely used in oil fields (commonly known as kowmachine). In foreign countries, this anti-partial grinding rotary shaft has become a standard equipment. It is called an "anti-partial-grinding solution" |
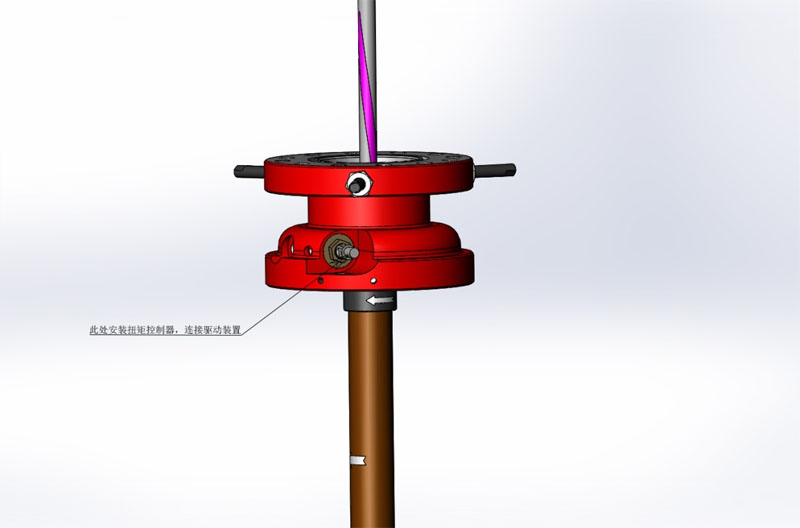 |
graph 01 |
|
The principle is very simple, is to let the pipe turn, at 7-10 times a day. So that the wear is evenly dispersed to the circumference of the pipe wall, that is, let the grinding points wear evenly along the circumference of the pipe wall, to achieve the purpose of extending the well repair cycle. In the early years, the structure is relatively simple, as shown in Figure 01, a ratchet wrench is connected behind the torque controller, the tail end of the ratchet wrench is connected to a cable chain, and the other end of the cable chain is connected to the furnace head, using the upper and lower movement of the furnace head to drive the ratchet wrench to move an Angle, FIG. 02. |
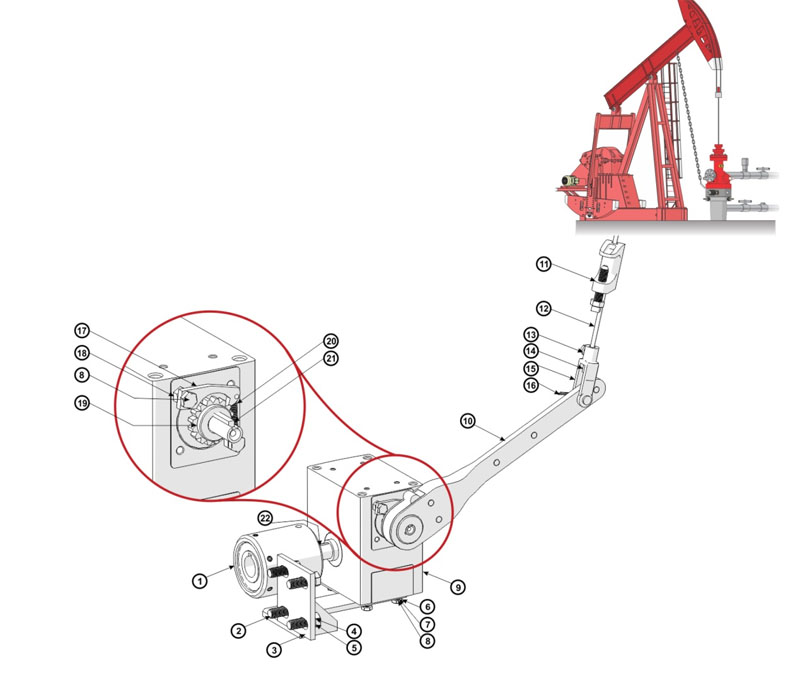 |
graph 02 |
|
Another method is to install an electric deceleration drive device with a large deceleration ratio behind the torque controller to drive the worm. This design is a classic, found in almost all installed anti-partial wear solutions around the world. As shown in view view 03 |
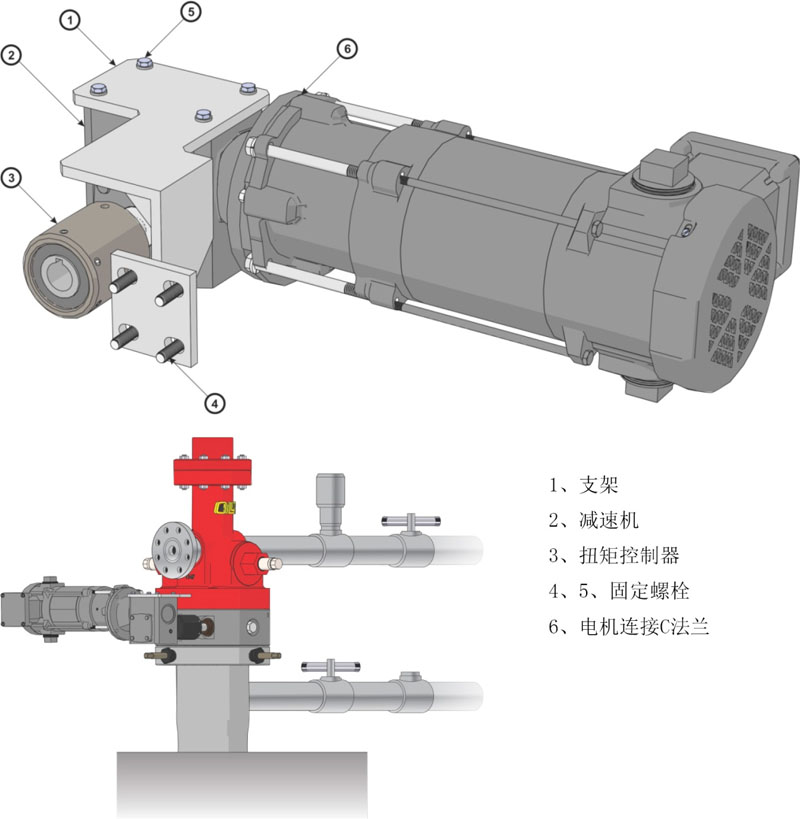 |
graph 03 |
|
|
1. Potential problems with the original design
In 2007-08, we participated in the improved design of the electric towing part, and implemented the new electric towing scheme. According to the foreign design assignment and the reference sample provided, a 400:1 gear reducer connected a 60:1 worm reducer, and the motor is 1 / 4 horsepower C flange NEMA motor. According to the feedback of later users, although the torque controller is used, the aluminum alloy shell of the 400:1 reducer is often bitten by the gear in the temporal use. We have found that due to the field of the working environment used in the device, the temperature is 40 ° C-minus 40 ° C, the gear is oil lubrication, the temperature change and processing and installation accuracy, the gear is biased in continuous operation. At the same time, due to the huge deceleration ratio, the power of the drive motor is too large, resulting in the partial load torque of the offset load gear is too large, far exceeding the strength of the aluminum alloy shell, thus resulting in the gear shaft being pried out. To solve this problem, we have done a lot of research, found the reason from the underlying logic, and obtained a number of national patents. |
|
2. design philosophy
We set the maximum torque of the tubing rotation of the anti-partial grinding solution as the maximum torque of the buckle thread on the tubing, and calculate the power to rotate the tubing for 5-7 times / day:
P=T*n/9550(kw )
n=rpm; T=N.M
We first select the most commonly used 2-7 / 8 " oil pipe, baosteel BG110S on the maximum allowable buckle for 5060N. M; The maximum torque of P110 is 2300N.M。
Take Baosteel as an example P=5060*6/24/60/9550=0.0022KW
Sky Steel P110 pipe P=2300*6/24/60/9550=0.001KW
Thus, the maximum allowable power to drive the tubing rotation is very small, only 1-2 watts. The original design uses a 1/4 horsepower motor to drag, and the output power is 100 times larger!
In recent years, with China's industrial robot and industrial automation, the popularization of intelligent, small wei type dc brushless planetary gear reduction motor popularization, make us have a revolutionary breakthrough in design, so, we approach, creatively using the world's unique built-in 24V dc brushless planetary gear drive mode, and the PLC. It realizes controllable adjustable torque, controllable adjustable speed, overload protection, fault alarm, and a series of functions that traditional machinery can not achieve. |
|
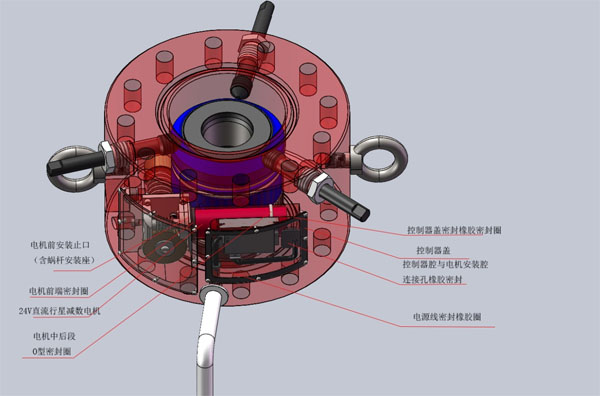 |
Figure 1 |
|
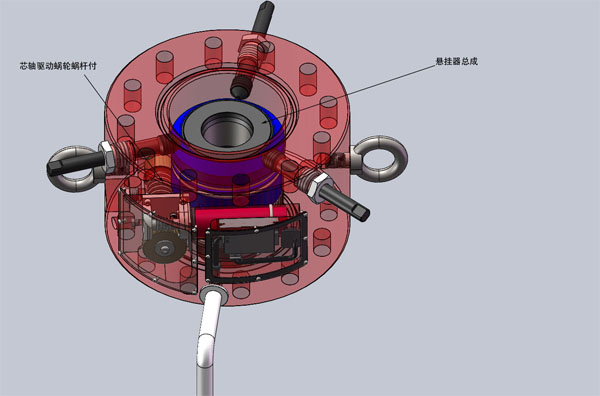 |
Figure 3 |
|
|
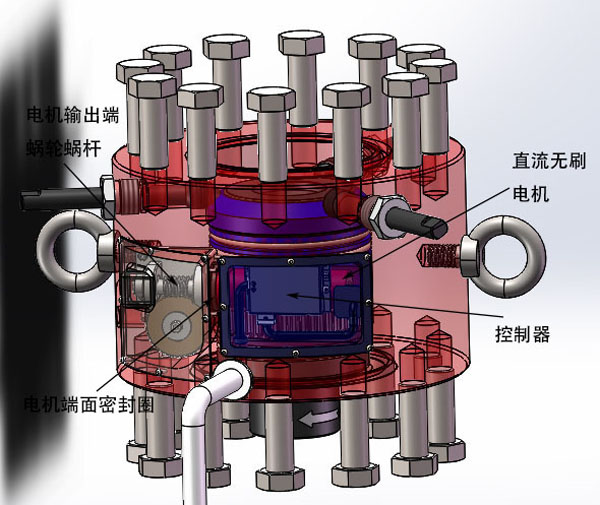 |
Figure 2 |
|
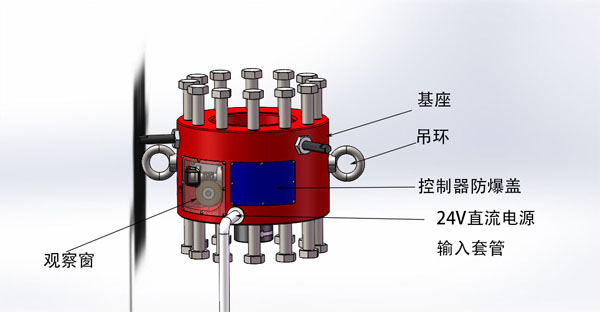 |
Figure 4 |
|
|
 |
Figure 5 |
|
|
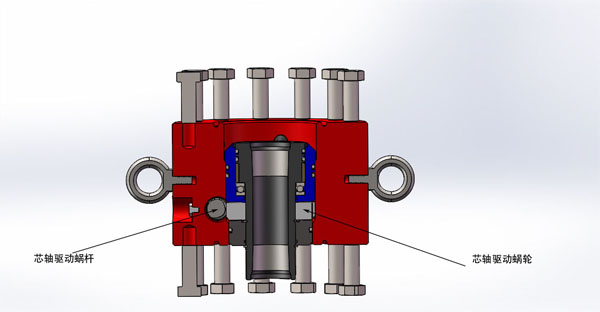 |
Figure 6 |
|
|
|
As shown in Figure 1, although the 24V brushless DC motor and the controller do not produce sparks, we take explosion-proof measures in the structure. Figure 2 and Figure 3, internal structure, motor output terminal, Figure 5, Figure 6, manrel drive principle. |
|
3. Calculation and setting of the parameters
The rated output torque of the motor is 15N.M |
|
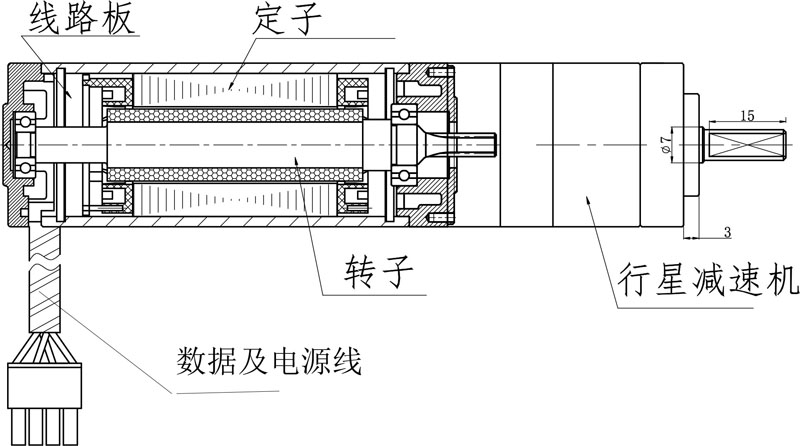 |
Figure 7 |
|
|
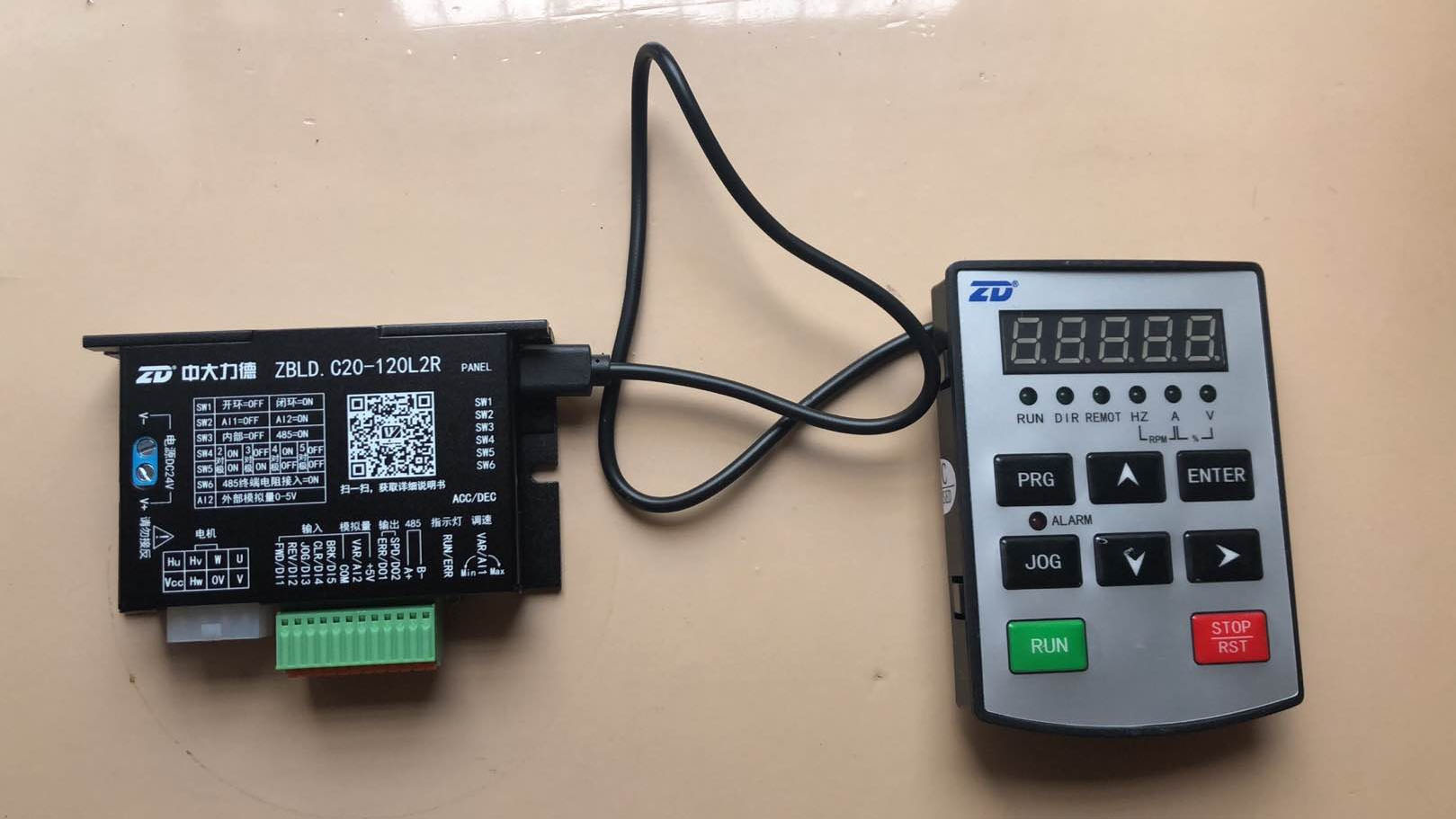 |
Figure 8 |
|
|
|
n The controller is a programmable industrial computer, for different specifications of tubing, the maximum allowable torque of the screw buckle is different, and the gap is very large. When the oil pipe rotation encountered resistance is greater than the maximum allowable torque of the oil pipe buckle, it must be stopped in time. Therefore, to set the controller before use, the keyboard code is illustrated as follows:
n F00.15=1 Restore the factory settings
n F02.04= Current limit value shall be set by customers according to different current values
n F07.00=010 Current overload shutdown
n F07.01=100100%
n F07.02=0.1 0.1s after overload
n The codes are detailed in the manual
n There are two modes of torque control, one is set according to the maximum allowable torque commonly used in China, and the other is set according to the user's own requirements. The first is that we provide a parameter table formulated according to the maximum allowable torque of commonly used tubing buckle in China. In the other, we provide an algorithm, which is a database made of Excel table, input the control torque you require and display the corresponding set parameters. |
|
4. Overview of anti-grinding solutions
R250 suitable for 250 diameter four-way head, 15 "(381mm), 9.38" (238mm), 12.5 "(317.5mm), 121-1 / 8" -8UN, or M30 thread, hole depth 1-3 / 8 "(35mm), suspension spindle thread 3.5" -8 EUE (or 3.5 "-10UN) outer threads (inner) and 2-7 / 8" -8 EUE (or 2-7 / 8 " -10UN, same). For 14 "(355.6) shaft core shaft, smaller diameter oil pipes can be connected through 2-7 / 8" inner threads.14 "rotor size is as follows: outer diameter: 14", height 9 ", thread center park diameter 11.5", 121 "-8 UNC thread, metal seal R45, with 15".
An anchor is installed on the well pump, therefore, a rotary ring must be installed in the upper section of the anchor. The following figure shows the structure and the downhole installation status |
|
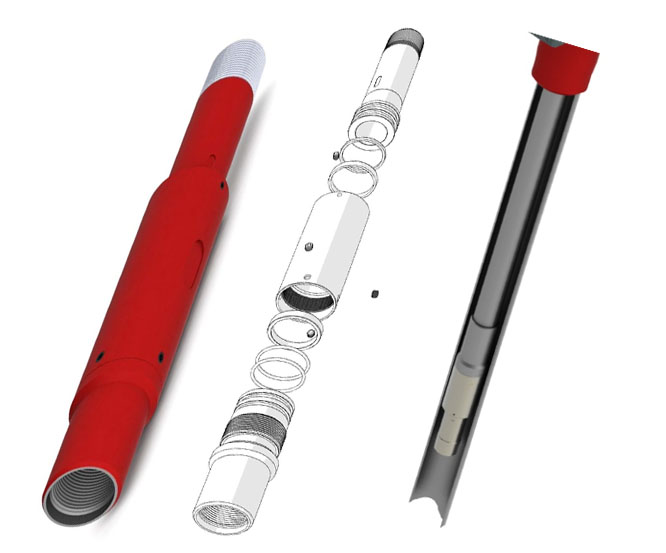 |
Figure 9 |
|
|
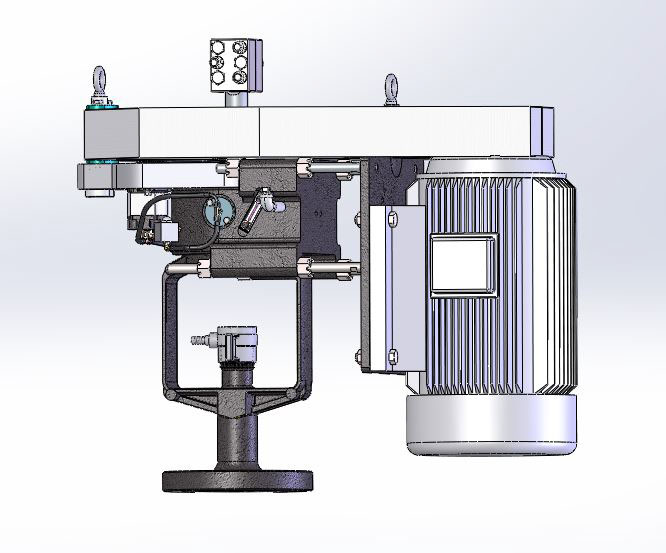 |
Figure 10 |
|
|
|
The rotating ring must be determined according to the specific structure and working principle of the anchor, so the downhole structure is the key. This tubing rotator is also suitable for screw pumps for our 30 HP head (separate data release). |
When the tubing rotates, the pumping rod will cause the tripping of the pumping rod. Therefore, in this solution, the pumping rod rotator must be added, and the speed of the pumping rod rotator is higher than that of the tubing rotator. In this way, the pumping rod rotator + tubing rotator + tubing rotation ring forms a complete set of anti-partial grinding solution. |
|
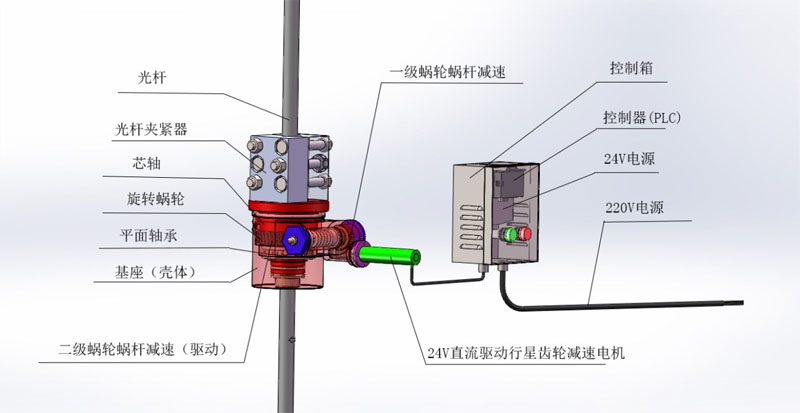 |
Figure 11 |
|
|
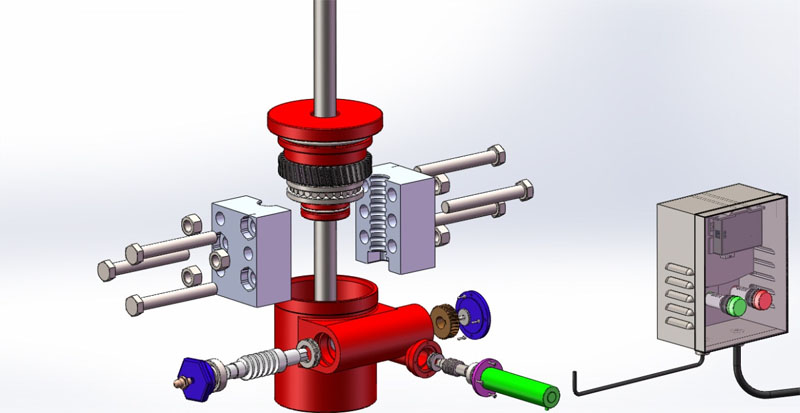 |
Figure 12 |
|
|
|
The pumping rod rotator is installed on the suspension rope device, and the driving principle and control mode are the same as the tubing rotator. The pumping rod rotator can be used alone. When used with the tubing rotator, the power management is: the pumping rod motor stops, the tubing rotator stops simultaneously; the tubing rotator motor stops, and the pumping rod rotator motor stops. |
|
5. Modular design
The motor and the first stage worm gear set and the controller can be quickly inserted and replaced.
|
|
6.The anti-partial grinding solution has the following characteristics
Suitable for modifying any existing well head
Exextend the service life of tubing
Reduce expensive well repair costs and production stoppage to avoid production losses.
Suitable for all downhole pump types
Observation windows are used for routine inspection.
According to the experience and requirements of foreign customers, parts maintenance can be replaced without removing the well head, which is simple and quick. To achieve minimum maintenance and on-site maintenance costs and extend the service life of the tubing. |
|
|
 |
|